A Pressing Issue: How ‘the vinyl revival’ has caught out the music industry during the pandemic
SDE investigates manufacturing delays
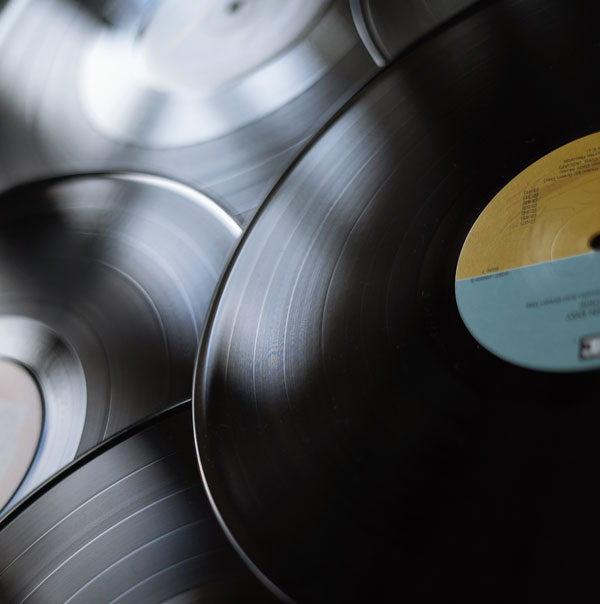
Release dates going back and back. Box sets getting postponed by a year. Physical albums arriving months after their digital release. Rumours of pressing plant meltdowns… COVID-19 was bound to have an effect on the release of albums. But the pandemic has brought home a crisis in the music industry, and that is, quite simply, the fact that there aren’t enough pressing plants to cope with the demand for vinyl.
On the surface, the figures for the so-called vinyl revival are healthy: even with the high street shut for most of the year, vinyl sales in the UK rose by nearly 10 percent to 4.8 million in 2020. It’s the 13th consecutive year that vinyl sales have risen. Sales of turntables grew too, as music fans who had previously resisted the headlines about ‘The Vinyl Revival’ finally succumbed and began rediscovering love for the black stuff.
Despite the rise in popularity, there has been no serious initiative, since vinyl sales picked up, to increase vinyl production. No new pressing plants of any significant size built in the past decade, coupled with an ever-increasing rise in sales, means a crisis point has been reached.
Where once the turnaround to get a record on the shelves was around six weeks, it’s now three-to-five months, or possibly even longer. Small wonder that several artists are now releasing their albums digitally first, before vinyl, CD and cassette versions arrive months later. It’s the equivalent of the paperback being published before the hardback, but it’s hard to blame the artists wanting fans to hear their album as soon as it’s finished. One of the first bands to pilot the split release were Sheffield rockers Bring Me The Horizon. They released their mini-album Post Human: Survival Horror digitally last October – and saw the album reach number one when the physical version arrived in January. As keyboardist Jordan Fish told SDE: “Our record label is quite quick. But, when we heard we’d have to wait 16 weeks for it to be out on vinyl, we put our foot down. That’s a fucking ridiculous wait, particularly because no-one has really been able to explain why it takes so long.”
It’s that lack of clarity which is frustrating for everyone – SDE included. We’ve been hearing rumours for months of key box set releases by some very big names postponed indefinitely. We’ve seen release dates for new albums slip back and back. And we’ve been wondering: just what is going to be the knock-on effect of pressing plants being at full capacity for months and months? Are the major labels really block-booking all the available capacity at these plants? Will the industry ever catch up? And what of the environmental impact of producing and shipping
In a major investigation, we spoke to artists, labels, record stores, the BPI and the pressing plants themselves to find out whether the vinyl revival is about to crash to a halt… or if a vinyl revolution 2.0 is on the way.
How does a vinyl release normally work?
When an album is mastered, a lacquer is cut. This is then sent off to the pressing plant where a test pressing is made. This is what labels and artists use to make sure the finished album quality is up to scratch. This can take around four weeks or so.
Once a test pressing is approved, it’s then time to get the specified production run of vinyl manufactured. The usual lead time was around six weeks is because, there’s no doubting, it’s a complex, time-consuming process. Consider a run of coloured vinyl; production must stop while the presses are cleaned, so that the next run of vinyl is unaffected (this is one of the reasons why coloured vinyl is more expensive to make – it takes more time). Even with the smoothest running plant, there are no shortcuts in terms of processes and procedures and nothing that can be done to reduce this time.
Why has the time shot up to around five months?
When COVID-19 struck, things became, understandably, pretty quiet for the music industry for about three or four months. One pressing plant exec told us: “When things began falling apart, we advised our clients it was the perfect time to press up their vinyl, as there was suddenly capacity available. We told them: ‘If you don’t do it now, by the traditional pre-Christmas busy period, it’s going to be mayhem.’ And that’s exactly what happened. More artists are making more product.”
Quite simply, there is no immediate availability at pressing plants, because there aren’t enough pressing plants.
Just how many pressing plants are there?
It’s a question nobody seems able to give a precise answer to. The BPI don’t have any data on the exact number in the UK, let alone worldwide. It’s safe to say there are fewer than 10 established worldwide plants of any meaningful size. These are:
- OPTIMAL: a high-end German plant described by the head of one mid-sized label as “the Rolls-Royce of pressing plants” for the quality of its vinyl. They are also regarded as the leaders in quality control. In addition, AIM head Peter Quicke – also co-CEO of Ninja Tune and founder of the music industry’s climate change campaign group Music Declares – praises Optimal for its environmentally-friendly approach. Quicke said: “Optimal have a good record on renewable energy.
- PALLAS: Another highly-respected German plant. It’s slightly smaller than Optimal, but has a similar record on quality control and environmental impact.
- GZ: Europe’s largest plant is also its most controversial, accused of caring far more about quantity than quality. The Czech plant has a dodgy record on the number of faulty pressings it manufactures. However, one plant source told SDE: “You have to know their strengths and weaknesses. They’re excellent at producing different vinyl editions, like colour and splatter vinyl. They also make CDs, so they can be a good one-stop shop. If you stay on top of their quality control, they’re very convenient.”
- MPO: A well-regarded French plant, who tend to work mostly with Sony.
- THE VINYL FACTORY: The largest British plant is mainly used for boutique releases, not least on The Vinyl Factory’s own label, specialising in small-run special editions of major albums. Pete Paphides’ label Needle Mythology use The Vinyl Factory.
- MUSIC INDUSTRY: The Dutch plant is the home of reissues label Music On Vinyl. It kept the faith when vinyl was at its nadir, with Music On Vinyl pressing many reissues for major labels. Despite MOV being a good label, the majors have mostly taken their reissues back in-house.
- SONY JAPAN: In 2017, Sony re-opened its Japanese pressing plant after 30 years, the clearest sign from a major that it wanted to do something about the vinyl revival.
And that, give or take some boutique plants such as Jack White’s five-year-old Detroit in-house plant at his Third Man record label, is that. Well-regarded Hertfordshire plant Vinyl Presents is said to be expanding, but it still won’t be as large as The Vinyl Factory, never mind Optimal or GZ. It doesn’t seem enough for an industry that’s kept on reviving for 13 years.
Sony, Universal and Warner started getting all their vinyl for the States pressed in Europe, then shipped back to the US. And that’s still going on. It’s meant even more delays for British releases
UK Label boss
What about American pressing plants?
American vinyl is a thorny issue. The vinyl renaissance hasn’t been as widespread in the States as in Britain. In general terms, a box set will sell about as many copies in the US as in the UK, so there’s obviously far fewer records being sold per capita Stateside. There isn’t a mass-market pressing plant on the scale of GZ, with American vinyl essentially pressed at a series of boutique plants.
While pressing plants in mainland Europe were affected at different points by COVID-related shutdowns, the US was hit especially hard. One UK label boss told SDE: “When America went into lockdown, you couldn’t get vinyl made in the States. Sony, Universal and Warner started getting all their vinyl for the States pressed in Europe, then shipped back to the US. And that’s still going on. It’s meant even more delays for British releases.”
How do pressing plants decide which records get pressed first?
Specialist firms, such as Key Prodution, act as ‘brokers’ for labels. As well as offering design and packaging services, they buy up space across the plants to offer their clients. Some labels may choose to do this in-house, while others use a broker who will have relationships with all the major pressing plants and can advise on how long the wait time is, while obviously keeping track of any cancellations leading to last-minute availability. Major labels will negotiate a guaranteed capacity and, in normal times, the vagaries of a changing release schedule means that slots can become available for others to stake a claim. But at the moment, capacity has been at maximum virtually ever since lockdown.
Are major labels buying up all the space at pressing plants?
That’s always the rumour. It was convincingly denied both by a major label exec we spoke to and a pressing plant. SDE was told: “It’s not true that majors are going to plants and demanding ‘Take everyone else off press, you have to press ours’”. It seems, the majors simply have more resources to be able to plan their releases further ahead and know when they need the plant space. But another label boss said “none of the indies could get a look in” once one major supposedly began buying all the remaining space at a European plant to compensate for the lack of vinyl being pressed in America.
What about CDs? Are there delays in making them too?
Nope. The format that industry would apparently like to die still takes approximately 10 days to manufacture. If you are looking for fancy gatefold card wallet packaging you are probably looking at an additional 10 days. That’s still significantly less time than four-five months, though. The BPI said: “With 16 million copies sold [last year], CD continues to show its resilience and play a key role in shaping chart success”.
What are the practical effects of pressing delays on planning reissues?
The bonus material included on a reissue is often planned as far as a year in advance. But that doesn’t mean you are ready to go. Once you know what you want to do there are still plenty of potential hazards. A compiler might be trying to locate a specific master tape (it took the best part of a year to locate the multi-tracks required for Steven Wilson to remix Tears For Fears The Seeds of Love in 5.1 surround sound), or be in search of the official version of an unreleased song that’s been circulating on bootlegs for years (and yet doesn’t seem to be in the label’s vaults). Crucially, the artist themselves may be negotiating their approval of the reissue for some months. Perhaps they want to promote their new album before considering any discussion of their 40-year-old demos, or are looking to renegotiate their royalty rate or agree terms with their publishers on future sync deals. Such financial negotiations are a reality. Perhaps the artist would love to search their cellar for that elusive demo, but won’t have time to look for months. The point is, with shorter lead times, product managers have the luxury of being able to leave it much later to deliver the assets for their reissue project, so the time required to work through tasks, like those mentioned above, isn’t necessarily a big deal. But not at the moment. For example, if you are working on a major global reissue for September, in mid-April you’ve effectively already missed the boat, if there’s any kind of sizeable vinyl element in your project! At the moment SDE knows of at least a dozen major releases which had been scheduled for Q4 this year, but which have already been bumped to 2022.
If vinyl takes so long, will labels be tempted to switch to streaming-only deluxe reissues?
That depends. The consensus in appears to be that the industry is still burned from the failure of trying digital-only reissues when iTunes downloads were at their height a decade ago. The established ethos states that reissues only appear to collectors, and collectors need something physical to collect. Streaming-only reissues in hip-hop are increasingly well-established, however. The head of a reissues label said: “Digital is how a sizeable proportion of hip-hop’s audience has always consumed music.” BMG recently reissued The Farm’s album Spartacus as a stream-only set for its 30th anniversary. In short, physical reissues are safe, but who knows what the future will bring.
Will the digital-first, physical-later split release model become a fixture?
Possibly. After the success of Post Human: Survival Horror, Bring Me The Horizon have no qualms about repeating the idea. Jordan Fish says: “If there’s another option, we’d consider it, but we’re just not going to sit on our music for four months. We’re happy Post Human: Survival Horror made number one when the vinyl went on sale, but that had nothing to do with splitting the release. Without sounding arrogant, we’d already had a number one album. For us, seeing our Spotify listenership figures rise is a more accurate measure of how we’re doing than chart positions. We wanted our music out as soon as possible, because the lyrics are timely and there’s the practicality of singles to consider. We’d already released the first single from Survival Horror when we heard about the four-month wait. If you take too long once that ball is rolling on an album campaign, you start to lose momentum.”
Will five-month lead times for vinyl become the norm, or will the industry catch up post-COVID?
Even once American pressing plants are fully operational again, SDE heard from some sources that labels have realised it’s cheaper to export vinyl back to the US from Europe than to use the States’ expensive pressing plants. In other words, this over-running of European plants might – and we emphasise might – be here to stay. Given that plants were mostly at capacity before that influx, it doesn’t paint the rosiest future. Even if pressing plants return to normal post-COVID, the delays will take a year to 18 months to catch up on. As one plant source said: “COVID exacerbated what was already a problem. It’d take a long time to catch up, even if things are fine. It’d only take one of the major plants to have a problem to throw everything back into chaos, unless capacity is increased.”
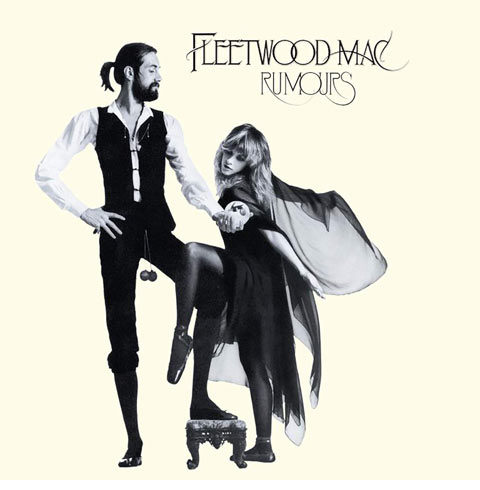
How are the delays in pressing albums affecting record stores?
Delays at getting fresh stock of popular titles in has gone from four weeks to four months. David Kosky, owner of well-respected record store Black Circle in Leighton Buzzard, Beds, saw albums by The Beatles, The Rolling Stones and Black Sabbath unavailable over Christmas. Even Fleetwood Mac’s eternal vinyl best-seller Rumours has been hard to stock. David said: “Warner’s account manager is very proactive at letting stores know when stock is coming back in. But Warner’s ordering portal for the whole of Europe had 16,000 vinyl copies of Rumours when that was last in. They went in a day. It was like trying to buy festival tickets online. It’s easier to stock for forthcoming releases, as they’ve got a street date to meet. But for restocks, albums go back and back. Other record stores are affected too, obviously, but it’s not ideal to knock back orders for albums like The Dark Side Of The Moon which are hardly obscure.”
Consumers like it, even if they moan about it
Label boss on Record Store Day
If record plants aren’t able to keep up with demand for regular albums, is going ahead with Record Store Day a good idea this year?
Absolutely, at least financially. It’s one of the biggest sales days of the year, for both stores and labels. “Consumers like it, even if they moan about it,” as one label boss neatly summarised. However, pressing plant delays is the main reason Record Store Day has again been split over two ‘drop’ days this year, on 12 June 12 and 17 July. Labels needed to have all their RSD titles at the plants by last October – and inevitable delays on some of RSD’s approximately 450 titles meant there needed to be a second date to accommodate the overspill.
The split dates creates more work for stores – a month to prepare, a month for each RSD and the month after to recover – and means Record Store Day will be the main focus of record shops for about a third of the year in 2021.
Black Circle’s David Kosky says: “I love Record Store Day, but some stores fall into a trap of bumbling along until RSD, having a massive weekend, then going back to bumbling along. It has to be approached as a nice supplement to the work you do the rest of the year. It’s important, but it can’t be to the detriment of your business as a whole.”
How has Brexit affected pressing plants?
It’s not been ideal. Because most plants are in Europe, getting vinyl to the UK is “an absolute nightmare,” according to the people at the sharp end we spoke to. Many couriers refuse to take goods to the UK. Costs for couriers and VAT issues have risen. Plants and their brokers have been hiring extra financial staff to understand the implications of Brexit and its paperwork. Crates of vinyl have been lost in transit. Warehouses are full, so there’s no room to leave any goods, vinyl included. “None of this is to do with pressing plant capacity,” as one source explained. “It all just adds to existing stress.”
What effect has that had on stores and labels?
Surprisingly little. It’s “an extra day or two” for UK titles to arrive, according to most of the labels we spoke to, echoed by the record stores. The pressing plants’ additional background work and stresses haven’t been passed on, in the main.
Are these delays going to increase the cost of vinyl?
According to Official Charts Company, the average retail price of an LP in 2020 was £21.55, compared to £20.23 in 2017. This includes boxsets. SDE readers may raise an eyebrow or two at these stats!
Shouldn’t the music industry have foreseen that some kind of problem was going to tip pressing plants over the edge?
Asking the music industry to foresee major issues is a tad naïve. In fairness, around five years ago, some plants did install new pressers to counteract a more minor version of the same issue. But it’s clear there needs to be a new plant to keep the vinyl revival in full swing.
Factories are incredibly expensive to build, it’s a massive, massive investment.”
Label executive
Will a new pressing plant get built to help solve the capacity problems?
This is the question at the heart of it all. Opinions vary. The BPI said: “We’re not aware of one being planned. That doesn’t mean it’s not being considered somewhere in the industry, we’re just not able to say one way or the other. It’s hard to say how productivity at the existing plants could be improved any further, as labels, distributors and so on have been working hard to achieve this already.” Pressing plants, their brokers and record stores would love to see it happen. But one label boss said: “Physical product, overall, is declining year on year and plants are very complex to run.” And a major label exec warned: “I don’t see a new plant happening. Factories are incredibly expensive to build, it’s a massive, massive investment.”
How could a new plant in Britain help?
It doesn’t seem especially likely that it’ll happen, but a new plant in the UK would at least overcome the issues plants face in exporting vinyl to the UK. It would also alleviate fears over albums leaking, both with the resulting turnaround time being shortened and for having fewer potential sources of someone leaking an artist’s music online. Label bosses admit that 90 percent of most leaks can be traced to a warehouse. Bring Me The Horizon’s 2013 album Sempiternal leaked two months before its planned release. Jordan Fish said: “Another reason we won’t wait four months to release an album is because the Sempiternal experience has left us paranoid about our music leaking. It doesn’t feel great to send your music outside of the country months ahead of release. I know NDAs are signed and I’m sure those distribution companies are great, but we can’t bear the thought of our music sat there for four months on a shelf. I’d have thought at least one label would take the opportunity at seeing how much vinyl is being sold and smash it by building a new plant. It definitely seems a good idea.”
It’s telling that a putative new UK pressing plant seemed to escape the attention of both the BPI and the record industry bosses we spoke to in preparing this feature. Based in Middlesbrough, the newly-launched Press On Vinyl hopes to press 100,000 records a month when it opens in May. Plant boss Danny Lowe told Teeside Live: “We hope we can help the fantastic local music scene. Not many towns have access to their own local vinyl plant, so it’s a real win for the area.” That’s undoubtedly laudable, but the ‘local’ aspect implies Press On Vinyl isn’t designed to help the worldwide vinyl pressing shortage.
Would a new pressing plant immediately solve everything?
No. One pressing plant source told us the complexities of getting a new plant up and running means it’d take a year to have any significant effect. SDE was told: “You don’t just install machines and everything is ready to go. You need a large boiler capacity, while pressers run differently depending on the air’s water content. There’s the galvanic side of making metalworks to make test pressings. You’d need six pressers to make a plant worthwhile, and finding trained engineers to run them isn’t easy. Every stage has a risk factor.”
The idea that 180g vinyl is better is purely emotional, because of its heaviness
Peter Quicke – CEO of Ninja Tune
What about the impact of vinyl on the environment? Should we be bringing more vinyl into the world?
The EU has regulations to make PVC (used in vinyl) less toxic. Music Declares Emergency wants pressing plants to use renewable energy. Founder Peter Quicke – also CEO of Ninja Tune and chair of AIM – said Optimal and Pallas are good on renewable energy, thanks partly to Germany’s beneficial renewable energy tariffs. Peter said: “All pressing plants are aware of the issues around sustainability. But, because of the current surplus demands on them, plants are currently focused on just being able to produce as much vinyl as they can. COVID has caused increased quality control problems because of staffing issues, so plants are struggling to think beyond the immediate.”
Those quality control problems means more records are being returned, and each ‘wasted’ vinyl is a big problem for the environment. Even recycled vinyl is made from the faulty stock on a production line before it gets into shops, rather than returned stock.
With most records being pressed in the EU, particularly with American plants closed, more records are being sent by air. “Ninja Tune uses sea freight where we can,” says Peter. “That takes four-six weeks, while air freight takes a day. If you’ve got a perceived ‘emergency’ of getting your record into the shops on time, air freight obviously makes more sense. The truth is, the diesel used in ships is nasty. But the amount of carbon is about five percent that of air freight.”
Does the music industry support the need for vinyl and pressing plants to become more sustainable?
“I think so,” says Peter Quicke. “But there’s some inertia and not enough urgency.” Another way to improve vinyl’s sustainability is to reduce heavyweight vinyl from 180g to 140g, as Ninja Tune have. Peter explains: “140g uses less PVC and it’s lighter, so you need less shipping. There’s also a rational reason why 140g vinyl sounds better: the stamper needs less pressure. The idea that 180g vinyl is better is purely emotional, because of its heaviness.”
Are CDs as damaging to the planet as vinyl?
They’re smaller and lighter, so they use less plastic and less shipping. But, as CDs are a mix of plastic and metal, they’re harder to recycle – though it can be done. CDs are also seen as more disposable than vinyl, so are more likely to end up on landfill. Vinyl is at least likely to be kept and played a lot, so it’s not single-use.
How else can productivity be improved, if a major new pressing plant isn’t being built?
Unearthing a previously undiscovered plant is obviously helpful: one US label recently learned of a plant in Nairobi. It’s also been mooted that cutting out record shops and going Direct-To-Consumer (D2C) would be beneficial, at least for labels. Delivery times are less strict, cutting out five weeks of distribution time. Vinyl and CDs go to one central warehouse, rather than to a distribution centre which sends it to hundreds of shops. Fans often get exclusive merchandise through a D2C webstore.
You Might Like
What are the disadvantages of D2C?
Anyone who’s used Rhino’s dismal Dig! store to buy their exclusive David Bowie and Iron Maiden live albums can answer that. Postage fees can be pricey, customer service is woeful and even securing the products can be a lottery. A friend of SDE is waiting for four of the five David Bowie live albums he managed to buy to turn up. Getting anyone at Dig! to respond to an email is a thankless task. It’s a far cry from a good record shop, as Black Circle’s David Kosky points out: “Labels starting to make albums and boxsets D2C-only makes it more difficult for shops like us but, if you dig into D2C sites, you don’t get value for money. Most fans aren’t bothered by the T-shirt or hat D2C albums get bundled with. Record shops aren’t just about the records, either. It’s social contact, discovering music in the shop, the cut-and-thrust of a customer community. D2C just can’t offer that.”
Is physical here to stay?
On a purely practical basis, physical is hugely beneficial to artists. Bring Me The Horizon’s Jordan Fish points out: “We sold over 10,000 physical copies of our album, which fans had been able to listen to for three months. Fans want to show support for their favourite artists. The truth is, if we’d released a T-shirt or a pendant instead of a vinyl to represent Post Human: Survival Horror and asked fans to buy that, a lot of them would have done so, because they want to support us. But vinyl is the ideal way to show that support. It’s playable, it’s the best audio experience, but we know of fans who buy our albums on vinyl who don’t have a turntable: it’s art, it’s something to get signed, a nice keepsake. Whichever way you want to approach it, vinyl is a great artistic product. No wonder there’s a big demand for it.”
Despite those cautionary words from labels about the expense of new pressing plants and the overall decline in physical product, the BPI insists it remains committed to the vinyl revival. They say: “We’re absolutely committed to vinyl. Labels, specialist and indie retailers, the recorded sector as a whole are hugely committed. Vinyl LPs account for 18 percent of all albums purchased, the highest level since the ’90s. Of course we’re committed to it.”
SDE investigation by John Earls & Paul Sinclair. Report by John Earls.
A record-like disk. It has an aluminium base plate attached to which is about 20mm of soft lacquer. Audio engineers using a lathe machine and a very sharp gemstone to carve the music into the lacquer.
Sync (or synchronisation) is a process where songs are combined with moving images – film, TV series, adverts, video games, trailers etc
Don’t ask. We’re sworn to secrecy!
By John Earls
158